Bridging the Imagination: Unveiling the Future of 3D Printing Materials Beyond Plastic
The world of manufacturing and design has witnessed a transformative revolution with the advent of 3D printing. Also known as additive manufacturing, 3D printing is a process that fabricates three-dimensional objects by layering materials based on a digital model. This groundbreaking technology has found applications across various industries, including aerospace, automotive, healthcare, and even fashion.
A New Dimension in Manufacturing
The significance of 3D printing lies in its ability to democratize production and bring customization to the forefront. Traditional manufacturing methods often involve time-consuming processes, costly tooling, and limited design flexibility. In contrast, 3D printing allows for rapid prototyping and on-demand production of complex geometries without the need for expensive molds or machinery.
Plastic’s Reign in the World of Additive Manufacturing
Since its inception, plastic materials have dominated the field of 3D printing due to their affordability, versatility, and ease of use. Popular plastic filaments such as Acrylonitrile Butadiene Styrene (ABS) and Polylactic Acid (PLA) have become staples in the industry. These materials offer a wide range of colors and properties suitable for various applications.
The prevalence of plastic in additive manufacturing can be attributed to its accessibility and familiarity among users, as well as its compatibility with most desktop 3D printers. However, despite their widespread use, plastic materials come with inherent limitations that hinder their potential for certain applications.
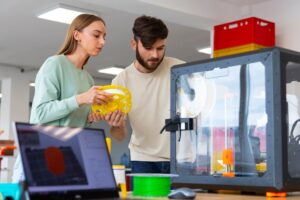
Limitations of Plastic Materials
While plastics are suitable for creating prototypes or low-stress components, they often lack the mechanical strength required for demanding industrial applications. Their durability may be compromised under extreme temperatures or stressors. Additionally, traditional plastics are not environmentally friendly since they are derived from non-renewable sources and contribute to plastic waste pollution.
Exploring Alternative Materials for Future Advancements
Considering the limitations of plastic, there is an urgent need to explore alternative materials that can unlock the full potential of 3D printing. By expanding the range of materials compatible with additive manufacturing, we can open doors to new applications and advancements in various industries.
The search for innovative materials goes beyond just finding substitutes for plastics. It involves investigating advanced materials that offer enhanced properties, such as strength, durability, temperature resistance, or biocompatibility.
These materials may enable the production of functional parts suitable for demanding fields like aerospace, healthcare, and architecture. This article delves into the future of 3D printing materials beyond plastic.
It explores emerging options such as metal-based alloys, ceramic composites, biodegradable polymers, and even hybrid material combinations. By understanding the potential breakthroughs offered by these alternatives, we can envision a promising future where additive manufacturing becomes more versatile, sustainable, and capable of revolutionizing how we design and fabricate objects.
Current State of 3D Printing Materials
Overview of commonly used plastic filaments (ABS, PLA)
Plastics have reigned supreme as the most widely used materials in 3D printing due to their versatility, affordability, and ease of use. Two names that stand out among plastic filaments are Acrylonitrile Butadiene Styrene (ABS) and Polylactic Acid (PLA). ABS is a popular choice for its durability and resistance to high temperatures, making it suitable for functional prototypes and end-use parts.
On the other hand, PLA has gained popularity due to its biodegradable nature derived from renewable resources like cornstarch or sugarcane. PLA is relatively easier to print with and offers excellent surface finish, making it ideal for aesthetic models and educational purposes.
Limitations and drawbacks of plastic materials (strength, durability, environmental impact)
Despite their wide usage in 3D printing, plastics do come with a set of limitations. One significant drawback lies in their strength and durability when compared to traditional manufacturing methods or alternative materials. Plastic parts printed using Fused Deposition Modeling (FDM) techniques can be prone to layer adhesion issues or break under high stress conditions.
Additionally, plastics such as ABS pose environmental concerns due to their non-biodegradable nature and the release of harmful fumes during the printing process. These limitations have paved the way for exploring alternative materials that can overcome these drawbacks.
Emerging materials beyond plastics (metals, ceramics, biodegradable polymers)
In recent years, 3D printing technology has witnessed remarkable advancements beyond traditional plastics into new frontiers by incorporating metals, ceramics, and biodegradable polymers as printable materials. Metal-based 3D printing has gained traction due to its ability to produce complex geometries with exceptional mechanical properties. Materials like titanium, stainless steel, and aluminum alloys have found applications in aerospace, automotive, and medical industries.
Ceramic-based 3D printing materials exhibit unique characteristics such as high-temperature resistance and electrical insulation, making them valuable for producing components in electronics and energy sectors. Furthermore, the growing demand for sustainable manufacturing has fueled the exploration of biodegradable polymers as alternative materials to tackle the environmental impact associated with plastic waste.
The current state of 3D printing materials is diverse and evolving rapidly. While plastics dominate the market due to their accessibility and affordability, they suffer from limitations in terms of strength, durability, and environmental sustainability.
However, emerging materials like metals, ceramics, and biodegradable polymers offer exciting possibilities for future developments in additive manufacturing. In the following sections of this article, we will delve deeper into these innovative materials to explore their potential applications and challenges ahead.
Innovations in Metal-Based 3D Printing Materials
Introduction to metal-based additive manufacturing techniques (powder bed fusion, directed energy deposition)
Metal-based 3D printing, also known as additive manufacturing, has revolutionized various industries by allowing the production of complex and customized components with exceptional precision. Two prominent techniques employed in metal-based additive manufacturing are powder bed fusion and directed energy deposition.
In powder bed fusion, a high-powered laser selectively melts and fuses layers of metal powder to form intricate structures. This technique is commonly used for creating high-strength metallic parts with intricate geometries.
On the other hand, directed energy deposition relies on depositing molten metal layer by layer using a nozzle or an electron beam. This technique is advantageous when producing large-scale components or repairing existing parts through additive processes.
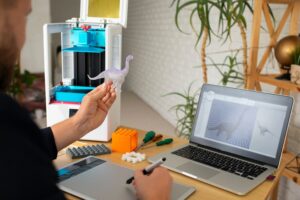
Advantages and applications of metal-based materials (aerospace components, medical implants)
Metal-based materials offer significant advantages over traditional plastics in terms of strength, durability, and heat resistance. The exceptional mechanical properties of metals make them ideal for critical applications in aerospace components and medical implants.
For instance, advanced alloys such as titanium and stainless steel are widely used in the aerospace industry due to their lightweight properties coupled with high strength-to-weight ratios. In the medical field, 3D-printed titanium implants have revolutionized orthopedic surgeries by providing patient-specific solutions that enhance bone integration and reduce implant rejection rates.
Challenges and ongoing research in improving metal-based 3D printing materials
Despite the remarkable progress made in metal-based 3D printing materials, several challenges persist that hinder their widespread adoption. One significant challenge is related to material quality control during the printing process itself, since factors like temperature gradients can lead to residual stress accumulation or defects within the printed object.
Researchers are actively working on optimizing process parameters to ensure consistency and reliability. Additionally, the high cost of metal powders used in additive manufacturing is another barrier to overcome.
Continuous efforts are being made to develop more cost-effective powder formulations without compromising on mechanical properties. Furthermore, enhancing the surface finish and post-processing techniques for metal-based 3D-printed parts remains an area of intensive research to eliminate post-build machining requirements and improve overall aesthetics.
Overall, metal-based 3D printing materials offer unparalleled possibilities for creating intricate and durable components in industries ranging from aerospace to medicine. Ongoing research aims to address the existing challenges and further refine these materials, making them more accessible, economical, and efficient for a wide range of applications.
Exploring the Potential of Ceramic-Based 3D Printing Materials
Overview of Ceramic Additive Manufacturing Processes: Extrusion-based, Binder Jetting
Ceramic-based additive manufacturing processes have opened up new avenues for creating intricate and functional objects. Two prominent techniques used in ceramic 3D printing are extrusion-based and binder jetting. Extrusion-based printing involves the deposition of ceramic pastes or slurries through a nozzle, layer by layer, to form the desired object.
This technique allows for the creation of complex geometries and is commonly used in architectural models and artistic sculptures. On the other hand, binder jetting employs a liquid binding agent that selectively bonds particles together to form solid ceramic structures.
Using this method, layers of powder are selectively bonded until the final object is achieved. It enables faster production times and is often utilized in industries such as aerospace and healthcare for prototyping components.
Unique Properties and Applications of Ceramic Materials: High-Temperature Resistance, Electrical Insulation
Ceramic materials possess remarkable properties that make them highly desirable for various applications in 3D printing. One such property is their exceptional high-temperature resistance, making ceramics suitable for manufacturing components that experience extreme heat or thermal stress, such as gas turbine parts or heat exchangers.
Additionally, ceramics provide excellent electrical insulation properties due to their low electrical conductivity. This characteristic makes them well-suited for producing insulators, electrical connectors, and even advanced electronic devices at a smaller scale.
Advancements in Ceramic Formulations for Enhanced Printability and Strength
To optimize ceramic materials’ printability and strength during additive manufacturing processes, significant advancements have been made regarding their formulations. Researchers have been focusing on developing ceramic powders with improved flow characteristics to enhance extrusion-based printing efficiency without compromising material integrity. Moreover, efforts have been directed towards achieving better control over particle size distribution and optimizing binder compositions in binder jetting techniques.
These innovations allow for greater control over the printing process, resulting in higher structural integrity and dimensional accuracy of the final ceramic objects. Furthermore, surface finishes and post-processing techniques have been improved to mitigate common issues such as cracking or warping during the printing and sintering phases.
Ceramic-based 3D printing materials offer unique properties and applications that go beyond the limitations of traditional plastic filaments. By utilizing extrusion-based and binder jetting processes, complex geometries can be achieved, making ceramics suitable for a wide range of industries including aerospace, healthcare, and electronics.
Ongoing advancements in ceramic formulations continue to improve printability, strength, and surface finishes of these materials. As technology progresses further, it is foreseeable that ceramic-based 3D printing will unlock even more possibilities for innovation across various sectors.
Biodegradable Polymers: Sustainable Future for 3D Printing?
Environmental concerns surrounding plastic waste generated by traditional 3D printing
Traditional 3D printing heavily relies on plastic materials, resulting in a significant environmental impact. The disposal of plastic waste generated from failed prints, support structures, and unused filament adds to the global pollution crisis.
This accumulation of non-biodegradable plastics in landfills poses a long-term threat to ecosystems and human health. Consequently, there is an urgent need to explore alternative materials that can mitigate these environmental concerns.
Introduction to biodegradable polymers as an eco-friendly alternative
Biodegradable polymers offer a promising solution to the environmental challenges posed by conventional plastic materials in 3D printing. These polymers are designed to degrade naturally over time through biological processes, minimizing their negative impact on the environment. Derived from renewable sources such as corn starch or algae, biodegradable polymers exhibit properties similar to traditional plastics while offering increased sustainability.
Applications and challenges in using biodegradable polymers for additive manufacturing
The potential applications for biodegradable polymers in additive manufacturing are vast. From producing consumer goods like packaging materials and household items to medical devices and prosthetics, these materials open up new possibilities for sustainable manufacturing across industries.
However, there are specific challenges associated with using biodegradable polymers in 3D printing processes. These include maintaining material stability during printing, ensuring mechanical strength comparable to traditional plastics, optimizing printability parameters, and managing post-processing techniques.
Conclusion
The future of 3D printing materials is undoubtedly evolving beyond plastic as new options emerge to address environmental concerns while expanding design possibilities. Biodegradable polymers provide a sustainable alternative to traditional plastics, allowing for eco-friendly additive manufacturing. Despite challenges related to stability and mechanical strength optimization, their potential applications are vast across various sectors.
Furthermore, the integration of different material types through hybrid structures pushes the boundaries of what is possible in additive manufacturing by creating objects with enhanced properties and functionality. By embracing these innovations in 3D printing materials and techniques, we can forge a path towards a more sustainable future that harmonizes technological advancement with environmental responsibility.