Building Brilliance: Unveiling the Architectural Revolution of 3D Printed Houses
The Rise of 3D Printing Technology: A Paradigm Shift in Manufacturing
The advent of 3D printing technology has ushered in a new era of innovation, transforming various industries and challenging traditional manufacturing methods. Initially developed as a rapid prototyping technique, 3D printing has evolved into a powerful tool that enables the creation of complex three-dimensional objects layer by layer.
This disruptive technology has revolutionized fields such as aerospace, medicine, and automotive manufacturing. With its ability to transform digital designs into physical objects with remarkable precision and efficiency, it was only a matter of time before the construction industry embraced this promising technology.
Introducing the Concept of 3D Printed Houses: Blending Vision with Reality
In recent years, the concept of 3D printed houses has gained significant attention due to its potential to reshape the way we build homes and structures. The idea behind 3D printed houses involves utilizing additive manufacturing techniques to construct dwellings directly from digital blueprints.
By employing large-scale robotic printers that extrude layers of specialized materials, these state-of-the-art machines can create walls, floors, and even intricate architectural features in a fraction of the time required by conventional construction methods. This groundbreaking approach holds immense promise for addressing housing shortages, reducing costs, enhancing sustainability efforts, and embracing innovative design possibilities.
Revolutionizing Construction from Digital Blueprints to Physical Buildings
The future of 3D printed houses embodies a transformative force within the construction industry. By harnessing advanced technologies like robotics and additive manufacturing processes, this emerging field offers tremendous potential for creating affordable homes with unprecedented speed and customization options.
As we delve deeper into how digital blueprints seamlessly translate into tangible structures through sophisticated machines, it becomes apparent that this paradigm shift will not only streamline construction practices but also push boundaries in terms of design possibilities and sustainable building practices. In this article, we will explore the intricacies of 3D printed houses, from the underlying technology to the innovative materials and techniques that make this future a tangible reality.
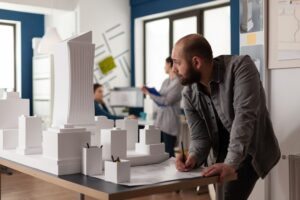
Understanding 3D Printed Houses
Explaining the process of 3D printing in construction
When it comes to the construction industry, 3D printing has emerged as a game-changer. This innovative technique, also known as additive manufacturing, involves creating three-dimensional objects by layering materials one on top of another. In the context of housing, 3D printed houses are built using large-scale robotic printers that extrude materials in a controlled manner to construct walls and structural elements.
This automated process eliminates the need for traditional forms of construction such as bricklaying or assembling prefabricated panels. By leveraging computer-aided design (CAD) software and advanced robotics, 3D printing in construction offers unprecedented accuracy and efficiency.
Overview of additive manufacturing techniques used in construction
Additive manufacturing techniques applied to construction encompass various methods tailored for different purposes. One widely used method is contour crafting, which involves extruding layers of concrete or other suitable materials through a nozzle guided by computer-controlled robotic arms.
Another technique called binder jetting utilizes powdered material that is selectively bound together by an adhesive or binder agent layer by layer until the final structure is formed. Additionally, large-scale volumetric additive manufacturing allows for the creation of entire building components off-site using specialized equipment and then assembling them on-site like building blocks.
Materials commonly used in 3D printed houses (concrete, plastic, etc.)
The choice of materials for 3D printed houses depends on factors such as structural requirements, affordability, and sustainability goals. Currently, one of the most prevalent materials used is concrete due to its strength and durability. Concrete mixtures specifically formulated for 3D printing ensure proper extrusion consistency during the building process.
Additionally, some projects explore using biodegradable plastics or recycled polymers that offer increased sustainability without compromising structural integrity. These materials enable the construction of sturdy, weather-resistant houses that meet regulatory standards while reducing the environmental impact associated with traditional construction.
Benefits and advantages of 3D printed houses
Creating homes through 3D printing technology presents a multitude of benefits that have the potential to transform the construction industry. Firstly, cost-effectiveness takes center stage as this method significantly reduces labor requirements by automating the construction process.
Compared to traditional methods, 3D printed houses can be built faster and with fewer workers, resulting in substantial cost savings. Moreover, this technology offers unparalleled customizability and design flexibility.
By digitally modeling structures before printing, architects and homeowners can easily modify designs to suit their preferences or incorporate complex geometries that would be challenging or costly using conventional techniques. Another remarkable advantage lies in the sustainable and eco-friendly aspects of 3D printed houses.
By optimizing material usage through precise layering, there is minimal waste generated during construction. Additionally, some projects explore using eco-friendly materials like recycled plastics or incorporating sustainable practices such as integrating renewable energy systems within the structure itself.
Furthermore, due to their efficient insulation properties and potential for incorporating smart technologies, 3D printed houses can achieve high energy efficiency ratings. By harnessing the potential of 3D printing in construction, we immerse ourselves in a world where affordability meets innovation, customization knows no bounds, and sustainability becomes an inherent aspect of building our homes for future generations to come.

From Digital Blueprint to Physical Building: The Process Unveiled
Initial planning and design phase
The transformation of a digital blueprint into a physical building starts with meticulous planning and design. Architects and engineers utilize sophisticated computer-aided design (CAD) software to create intricate digital blueprints that serve as the foundation for the 3D printed house.
This process allows for precise customization, enabling the incorporation of architectural features and structural elements into the design. From elegant curves to complex geometries, CAD software empowers designers to push boundaries and unleash their creativity while ensuring structural integrity.
Preparing for construction with digital fabrication technologies
Once the digital blueprint is finalized, it needs to be translated into machine-readable instructions that can be executed by 3D printers. The first step in this process is slicing the model into layers suitable for printing.
Slicing involves dividing the virtual model into numerous horizontal layers, each representing a cross-section of the final structure. Subsequently, these layers are transformed into machine instructions known as G-code, which specifies parameters such as nozzle movement, material deposition speed, and layer height.
Slicing the model into layers for printing:
Accurate slicing is crucial in ensuring precise layer deposition during construction.
Generating G-code instructions for the printer:
G-code acts as an intermediary language between CAD software and 3D printers, providing detailed instructions on how each layer should be printed.
On-site assembly using large-scale robotic printers
With digital blueprints converted into machine-readable instructions, it’s time for on-site assembly using advanced robotic printers capable of executing large-scale construction tasks. These printers often take the form of mobile robotic arms or gantries equipped with extrusion-based technology that deposits layers of material systematically. The extrusion-based approach involves precisely controlled deposition of cementitious or polymer-based materials in continuous lines, gradually building up the structure layer by layer.
Overview of mobile robotic arms or gantries used for printing walls and structures:
The use of mobile robotic arms or gantries enables efficient and precise printing, minimizing manual labor requirements while maintaining construction quality.
Extrusion-based printers depositing layers of material:
The extrusion process involves the controlled release of material through a nozzle, allowing for the gradual buildup of structural elements with high accuracy and reliability.
Robotic arms with multiple degrees of freedom enabling complex geometries:
Advanced robotic arms possess multiple degrees of freedom, granting them the ability to navigate intricate three-dimensional spaces. This capability facilitates the construction of complex architectural designs that were previously challenging to realize using traditional methods.
Conclusion
As we peer into the future of construction, 3D printed houses offer immense promise in transforming digital blueprints into stunning physical structures. From initial planning and design through cutting-edge digital fabrication technologies to on-site assembly using state-of-the-art robotic printers, every stage exemplifies a paradigm shift in construction methodology.
The innovations in materials and techniques open doors to unprecedented design possibilities while ensuring enhanced structural integrity.
With each passing day, we inch closer to a world where 3D printed houses become commonplace—a future where affordable housing solutions blend seamlessly with sustainable practices. Embracing this technology holds vast potential not only in revolutionizing architecture but also in addressing global housing challenges with creativity and efficiency.