Building the Future: Unveiling the Astonishing Transformation of Industries through 3D Printing
To truly comprehend the magnitude of the 3D printing revolution, one must first grasp the essence of additive manufacturing and its transformative impact on numerous industries. Additive manufacturing, commonly referred to as 3D printing, is a revolutionary process that builds three-dimensional objects layer by layer using digital designs.
Unlike traditional subtractive manufacturing techniques that involve cutting or drilling away material from a solid block, 3D printing adds material layer by layer, resulting in highly precise and complex structures.
Definition of 3D printing and additive manufacturing
At its core, 3D printing encompasses a range of technologies that enable the creation of physical objects directly from digital models. The process begins with a three-dimensional design file created through computer-aided design (CAD) software or obtained from existing digital models.
This digital representation is then sliced into numerous thin cross-sectional layers, which serve as instructions for the 3D printer to construct the object. Additive manufacturing, on the other hand, is a broader term that encompasses various techniques used in creating objects through the successive addition of materials.
While 3D printing is one popular method within this realm, it also includes processes like laser sintering and binder jetting. The common thread connecting these methods is their ability to fabricate intricate designs and structures by adding materials rather than removing them.
Overview of the 3D printing revolution and its impact on industries
The advent of additive manufacturing has heralded an era of unparalleled possibilities across industries. What was once considered science fiction has now become an integral part of modern manufacturing processes.
The potential impact spans domains such as aerospace and defence, healthcare, automotive production, architecture, fashion design, education, and beyond. This breakthrough technology holds immense promise for improving efficiency while reducing costs in various sectors.
By eliminating many of the limitations associated with traditional manufacturing, 3D printing enables businesses to produce complex geometric shapes, intricate internal structures, and customized designs that were previously unattainable. This revolution in production methods has set the stage for an accelerated pace of innovation and a shift towards more sustainable manufacturing practices.
As we delve deeper into the intricacies of 3D printing and its applications within different industries, it becomes evident that this technology has the potential to reshape our world in unprecedented ways. From enabling rapid prototyping to providing on-demand spare part production, additive manufacturing is empowering industries to push boundaries and reimagine what is possible.
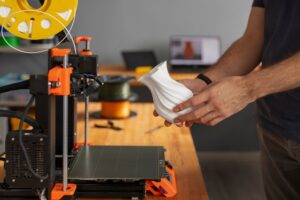
History of 3D Printing
Origins of Additive Manufacturing in the 1980s
The concept of additive manufacturing, or 3D printing, was first introduced in the 1980s. It emerged as a groundbreaking manufacturing technique that enabled the creation of three-dimensional objects through layer-by-layer deposition of materials.
The early pioneers in this field were Charles Hull and Scott Crump, who independently developed two influential technologies: stereolithography (SLA) and fused deposition modelling (FDM), respectively. These breakthroughs marked the beginning of a new era in manufacturing, where physical objects could be created directly from computer-aided design (CAD) models.
Early Applications and Limitations
Although additive manufacturing showed immense potential from its inception, its early applications were relatively limited due to several factors. One major limitation was the high cost associated with acquiring and operating the necessary equipment. Additionally, the available printing materials were restricted to certain polymers, which limited their applicability across industries.
Another challenge was the slow printing speed and limited resolution capabilities at that time. However, despite these limitations, early adopters recognized the value of 3D printing technology for rapid prototyping purposes.
It facilitated faster iteration cycles for product development by allowing engineers to swiftly convert digital designs into physical models. This application proved particularly beneficial in industries such as automotive, aerospace, and consumer goods.
Technological Advancements Leading to Widespread Adoption
Over time, significant technological advancements have propelled additive manufacturing into widespread adoption across various industries today. A key breakthrough came with advancements in machine speed and resolution capabilities during the late 1990s and early 2000s. This allowed for more intricate designs with higher levels of detail.
Furthermore, innovations in materials science expanded the range of printable materials beyond plastics to include metals, ceramics, and even biocompatible substances. This broadened the scope of applications for 3D printing in industries like healthcare, where personalized medical devices and prosthetics could be produced.
The advent of open-source hardware and software also played a crucial role in democratizing access to 3D printing technology. It spurred innovation, collaboration, and knowledge sharing within the additive manufacturing community, leading to an exponential growth of ideas, applications, and advancements.
As a result of these developments, additive manufacturing has evolved from a niche technology to a disruptive force that is profoundly transforming industries worldwide. The next sections will delve into specific industries that have been revolutionized by this game-changing technology.
Key Technologies and Processes in 3D Printing
Fused Deposition Modeling (FDM)
Under this particular umbrella of additive manufacturing, Fused Deposition Modeling (FDM) stands as one of the most widely used techniques. FDM works by extruding a filament of thermoplastic material, typically ABS or PLA, through a heated nozzle.
The nozzle moves in a controlled manner, depositing thin layers of the molten material onto a build plate. As each layer cools and solidifies, it bonds with the previous layer, gradually building up the desired object.
FDM technology offers several advantages, such as its affordability, simplicity of operation, and compatibility with a wide range of materials. Its versatility extends to various applications, including prototyping, architectural modelling, consumer goods production, and even educational purposes.
Stereolithography (SLA)
Stereolithography (SLA) is an additive manufacturing process that relies on photopolymerization to create 3D objects. In this technique, an ultraviolet laser beam selectively targets specific regions within a vat of liquid resin. When struck by the laser’s energy, the photosensitive resin solidifies into thin layers that form the desired object’s shape.
SLA technology allows for intricate details and high levels of precision due to its fine-resolution capabilities. It finds use across multiple industries, ranging from jewellery making and dental prosthetics to architecture and engineering, where intricate models or parts are necessary.
Selective Laser Sintering (SLS)
Selective Laser Sintering (SLS) is an additive manufacturing process that utilizes lasers to fuse powdered materials layer by layer to create solid objects. During SLS printing, a high-powered laser selectively scans cross-sections of powdered material contained within a build chamber according to a 3D model’s specifications.
This localized heat exposure causes the particles to fuse, forming a solid layer. As the process continues, a mechanism lowers the build platform incrementally, and fresh powder is added to create subsequent layers.
SLS technology has found remarkable applications in various industries. It is particularly valued for creating complex geometries, functional prototypes, intricate parts for aerospace applications, automotive components, and even medical implants due to its ability to work with a wide range of materials, including metals and engineered plastics.

Industries Transformed by Additive Manufacturing
Aerospace and Defense
Revolutionizing the aerospace and defence industries, additive manufacturing has opened up a world of possibilities. One significant application lies in the use of lightweight, complex parts in aircraft manufacturing.
With traditional manufacturing methods, producing intricate components with minimal weight poses significant challenges. However, 3D printing allows for the creation of intricate designs that reduce weight without compromising strength or functionality.
This enables aerospace companies to enhance fuel efficiency while maintaining structural integrity. Furthermore, additive manufacturing offers unparalleled customization possibilities for military equipment.
From firearms to tactical gear, 3D printing enables rapid prototyping and on-demand production of custom parts tailored to individual needs and preferences. This flexibility empowers defence forces to swiftly adapt their equipment to evolving mission requirements while optimizing performance and functionality.
Healthcare
In the realm of healthcare, additive manufacturing has emerged as a game-changer by facilitating groundbreaking advancements in medical device production. By leveraging 3D printing technologies, healthcare professionals can create highly intricate medical devices with enhanced precision and accuracy. This enables customization based on patients’ unique anatomical needs.
Moreover, additive manufacturing plays a pivotal role in creating customized prosthetics for amputees. Traditional prosthetics often come with limitations regarding fit and comfort due to standardized design practices.
However, 3D printing allows for personalized prosthetic solutions that perfectly align with an individual’s body structure and functional requirements. This not only improves patient comfort but also enhances mobility and quality of life for those reliant on prosthetic limbs.
Automotive
The automotive industry has been significantly impacted by additive manufacturing in various aspects of its operations. One prominent area is rapid prototyping for car design.
Traditional prototyping involves time-consuming processes such as moulding and tooling, resulting in high costs and lengthy development cycles. However, 3D printing enables the quick production of physical prototypes directly from digital designs.
This expedites the design iteration process, allowing automotive manufacturers to refine their products more efficiently. Furthermore, additive manufacturing enables on-demand spare parts production in the automotive sector.
Instead of relying on complex supply chains and warehouses filled with a vast array of spare parts, car manufacturers can now leverage 3D printing technologies to produce components as needed. This reduces inventory costs while ensuring a steady supply of necessary parts, even for models that are no longer in active production.
By transforming aerospace and defence manufacturing processes, revolutionizing medical device creation in healthcare, and streamlining prototyping and spare parts production in the automotive industry, additive manufacturing is reshaping various sectors like never before. The possibilities offered by 3D printing continue to push boundaries and unlock new opportunities for innovation across industries worldwide.
Advantages and Challenges in the Adoption of Additive Manufacturing
A. Advantages:
Reduction in Material Waste: One of the most significant advantages of additive manufacturing is its ability to minimize material waste. Traditional manufacturing methods often require subtractive processes, where excess materials are cut away from a larger block, resulting in significant waste. In contrast, 3D printing builds objects layer by layer, using only the necessary amount of material. This efficient use of resources not only reduces costs but also contributes to sustainable practices by minimizing environmental impact.
Faster Production Times: Additive manufacturing offers an exceptional advantage when it comes to time efficiency. In traditional manufacturing processes, creating complex geometries often involves multiple steps and assembly processes that can be time-consuming. With 3D printing, intricate designs can be produced as a single piece without the need for separate components or extensive assembly. This streamlined process eliminates production bottlenecks, reduces lead times, and allows for faster product iterations, enabling companies to respond more quickly to market demands and stay ahead of their competitors.
Design Freedom: Additive manufacturing provides unparalleled design freedom compared to traditional manufacturing techniques. The layer-by-layer building approach enables the production of highly complex shapes and structures that would be nearly impossible or cost-prohibitive using conventional methods. Designers can innovate without constraints imposed by traditional tooling limitations, enabling them to create intricate geometries and lightweight structures with internal lattice support systems for enhanced functionality and performance.
B. Challenges:
High Initial Costs: Implementing additive manufacturing technologies often requires a significant initial investment in equipment, software licenses, and employee training—an obstacle that may deter some businesses from adoption. However, it is essential to consider the long-term cost benefits associated with additive manufacturing, such as reduced material waste and improved production efficiency, which can lead to substantial savings over time.
Limited Material Options: While the range of materials suitable for 3D printing is continually expanding, it currently remains more limited compared to traditional manufacturing processes. However, advancements in material science are rapidly addressing this challenge. Researchers and industry leaders are developing new materials with enhanced properties like strength, flexibility, conductivity, and more, expanding the possibilities for additive manufacturing applications across industries.
Intellectual Property Concerns: As additive manufacturing becomes more accessible and widespread, concerns about intellectual property (IP) protection arise. The ease of reproducing physical objects through 3D scanning and printing poses a risk of unauthorized replication or counterfeiting of patented products. Protecting IP in this digital age requires robust strategies that involve legal frameworks, secure file encryption methods, watermarking techniques, and diligent monitoring to prevent unauthorized use or infringement. By weighing the clear advantages of reduced material waste, faster production times, and design freedom against challenges such as high initial costs, limited material options, and IP concerns, businesses can make informed decisions on incorporating additive manufacturing into their operations.
Future Trends in Additive Manufacturing
1. Pushing the Boundaries of Materials
Expanding Horizons of Material Capabilities As additive manufacturing continues to evolve, one of the most exciting future trends lies in pushing the boundaries of materials that can be used for 3D printing. Currently, a wide range of materials, such as plastics, metals, ceramics, and even food products, can be printed. However, researchers and engineers are actively exploring new materials with unique properties that can revolutionize various industries. For example, advancements in bioprinting are paving the way for printed organs and tissues that could potentially transform healthcare by addressing organ transplant shortages. Moreover, ongoing research focuses on developing innovative composite materials that possess enhanced strength or conductivity properties for applications in the aerospace and electronics industries.
2. Integration of Artificial Intelligence (AI)
Unleashing the Power of AI into Additive Manufacturing Artificial Intelligence (AI) is poised to play a significant role in shaping the future of additive manufacturing. Through machine learning algorithms and predictive analytics, AI can optimize designs to enhance efficiency while minimizing material waste. By analyzing vast amounts of data from previous prints and incorporating user feedback, AI algorithms can generate optimized designs with improved performance characteristics and reduced production time. Additionally, AI-powered algorithms will enable machines to self-monitor their performance during printing processes and make real-time adjustments to ensure high precision and quality output.
Conclusion
The 3D printing revolution brought about by additive manufacturing has transformed multiple industries with unprecedented possibilities for customization, rapid prototyping, and increased efficiency. As we look towards future trends in this field, it becomes evident that there is no limit to what additive manufacturing can achieve.
From exploring new frontiers in material capabilities to integrating artificial intelligence into printing processes for enhanced optimization, these advancements hold great potential for disrupting industries across the globe. As additive manufacturing continues to evolve, we can anticipate even more exciting and groundbreaking applications that will revolutionize the way products are designed, manufactured, and consumed.
With each passing day, we step closer to a future where additive manufacturing becomes an integral part of our lives, revolutionizing the way we create, innovate, and solve complex challenges. The possibilities are truly limitless.