Integration of 3D printing into the space industry for satellite and spacecraft manufacturing
The integration of 3D printing into the space industry has revolutionized the way satellite and spacecraft manufacturing is carried out. Also known as additive manufacturing, 3D printing is the process of building three-dimensional objects by adding layer upon layer of material. It has transformed the traditional manufacturing process by allowing the creation of complex and intricate designs with ease.
In the space industry, 3D printing has found a variety of applications, from printing spare parts for spacecraft, to manufacturing entire satellites. The benefits of using 3D printing technology in the space industry are numerous, including reduced manufacturing time and costs, increased design flexibility, and improved efficiency.
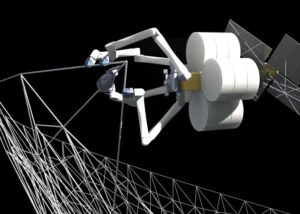
One of the most significant benefits of using 3D printing technology in the space industry is the reduction in manufacturing time and costs. Traditional manufacturing methods, such as injection molding, can be time-consuming and expensive. 3D printing, on the other hand, can produce complex designs in a matter of hours, and at a lower cost. This is especially important in the space industry, where time and cost are critical factors.
Another benefit of 3D printing in the space industry is the increased design flexibility. The traditional manufacturing process limits the design options available due to the limitations of the manufacturing process. 3D printing, on the other hand, allows for the creation of highly intricate designs that would be impossible to produce using traditional manufacturing methods. This allows for the creation of satellites and spacecraft with improved performance and capabilities.
In addition to reducing manufacturing time and costs and increasing design flexibility, 3D printing also improves efficiency in the space industry. The use of 3D printing technology allows for the creation of parts and components that are lighter and stronger than their traditionally manufactured counterparts. This is important in the space industry, where every gram of weight counts. Lighter and stronger components allow for the creation of spacecraft and satellites with improved performance and reliability.
One of the most notable examples of the use of 3D printing in the space industry is NASA’s use of the technology to manufacture rocket engine parts. In 2013, NASA successfully tested a rocket engine that contained 3D printed parts. The engine was able to produce more power while using less fuel than previous engines, thanks to the lighter and stronger 3D printed parts. This is just one example of the many ways that 3D printing technology is transforming the space industry.
Another application of 3D printing in the space industry is the creation of satellite components. Satellites are complex machines that require a wide variety of parts and components to function. With 3D printing technology, these parts and components can be manufactured quickly and efficiently, allowing for the creation of satellites with improved capabilities and performance. In addition, 3D printing technology allows for the creation of satellite components that are customized to fit specific mission requirements.
3D printing is also being used to manufacture small satellites known as CubeSats. CubeSats are small, low-cost satellites that are designed to carry out a variety of missions, from scientific research to communications. With 3D printing technology, CubeSats can be manufactured quickly and efficiently, allowing for the creation of large constellations of satellites at a lower cost than traditional manufacturing methods.
Despite the many benefits of 3D printing in the space industry, there are also some challenges that need to be addressed. One of the main challenges is the need to ensure that 3D printed parts and components are reliable and meet strict safety standards. In addition, the use of 3D printing technology in the space industry requires a high level of expertise and specialized equipment.
One of the most significant advantages of using 3D printing in the space industry is the reduction in manufacturing time and costs. Traditional manufacturing methods can be time-consuming and expensive, while 3D printing can produce complex designs in a matter of hours and at a lower cost. This is especially important in the space industry, where time and cost are critical factors.
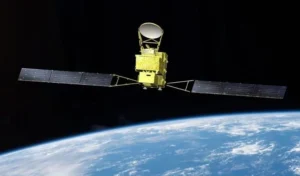
Furthermore, 3D printing offers increased design flexibility. Traditional manufacturing methods limit the design options available due to the limitations of the manufacturing process. 3D printing, on the other hand, enables the creation of highly intricate designs that would be impossible to produce using traditional manufacturing methods. This allows for the creation of satellites and spacecraft with improved performance and capabilities.
In addition to reducing manufacturing time and costs and increasing design flexibility, 3D printing also improves efficiency in the space industry. The use of 3D printing technology allows for the creation of parts and components that are lighter and stronger than their traditionally manufactured counterparts. This is important in the space industry, where every gram of weight counts. Lighter and stronger components allow for the creation of spacecraft and satellites with improved performance and reliability.
One of the most notable examples of the use of 3D printing in the space industry is NASA’s use of the technology to manufacture rocket engine parts. In 2013, NASA successfully tested a rocket engine that contained 3D printed parts. The engine was able to produce more power while using less fuel than previous engines, thanks to the lighter and stronger 3D printed parts. This is just one example of the many ways that 3D printing technology is transforming the space industry.
Another application of 3D printing in the space industry is the creation of satellite components. Satellites are complex machines that require a wide variety of parts and components to function. With 3D printing technology, these parts and components can be manufactured quickly and efficiently, allowing for the creation of satellites with improved capabilities and performance. In addition, 3D printing technology allows for the creation of satellite components that are customized to fit specific mission requirements.
3D printing is also being used to manufacture small satellites known as CubeSats. CubeSats are small, low-cost satellites that are designed to carry out a variety of missions, from scientific research to communications. With 3D printing technology, CubeSats can be manufactured quickly and efficiently, allowing for the creation of large constellations of satellites at a lower cost than traditional manufacturing methods.
Despite the many benefits of 3D printing in the space industry, there are also some challenges that need to be addressed. One of the main challenges is the need to ensure that 3D printed parts and components are reliable and meet strict safety standards. In addition, the use of 3D printing technology in the space industry requires a high level of expertise and specialized equipment.
Moreover, the materials used in 3D printing are still limited, which restricts the use of this technology in the space industry. For example, materials that can withstand extreme temperatures and radiation exposure are essential for space applications, and not all 3D printing materials can meet these requirements. Therefore, more research is needed to develop new materials that meet the demands of the space industry.
Conclusion
In conclusion, the integration of 3D printing into the space industry has transformed the way satellite and spacecraft manufacturing is carried out. The benefits of using 3D printing technology in the space industry are numerous, including reduced manufacturing time and costs, increased design flexibility, and improved efficiency. Despite some challenges that need to be addressed, 3D printing is rapidly becoming an essential part of the space