From Conception to Creation: Unveiling the Evolutionary Odyssey of 3D Printing in Product Design
In the realm of innovative technologies, 3D printing has emerged as a groundbreaking phenomenon that promises to revolutionize the field of product design. Its ability to transform digital prototypes into tangible objects with astounding precision and complexity is reshaping traditional manufacturing processes.
At its core, 3D printing, also known as additive manufacturing, involves building three-dimensional objects layer by layer, directly from digital models. This article aims to explore the evolving role of 3D printing in product design and shed light on its significance in shaping the future of manufacturing.
Definition of 3D Printing and its Significance in Product Design
3D printing is a versatile manufacturing technology that enables the creation of physical objects by depositing successive layers of material based on a digital design. Unlike traditional subtractive methods, where materials are removed from a solid block to create a desired shape, 3D printing offers an additive approach that allows for greater flexibility and complexity in design. This technology holds immense significance in product design as it empowers designers with the ability to rapidly prototype their ideas, test functionality, and make necessary iterations before final production.
Overview of the Evolution of 3D Printing Technology
The evolution of 3D printing technology can be traced back to its inception in the early 1980s when Chuck Hull invented Stereolithography (SLA), which paved the way for rapid prototyping. SLA involved using ultraviolet light to selectively cure successive layers of liquid resin into hardened plastic components.
Since then, numerous advancements have been made in both hardware and software domains for additive manufacturing. From Selective Laser Sintering (SLS) utilizing powder materials to fused deposition modeling (FDM) employing filament-based extrusion techniques, each iteration propelled this technology forward.
The evolution didn’t stop there, as materials science played a crucial role in expanding the capabilities of 3D printing. Initially limited to plastics, the repertoire now includes metals, ceramics, photopolymers, and even living tissues.
This broadening range of materials has facilitated the production of functional prototypes and end-use parts across various industries. Moreover, with advancements in computer-aided design (CAD) software, designers can create intricate and detailed digital models that can be translated into physical objects with unprecedented accuracy.
The seamless integration of CAD with 3D printing technology has streamlined the design process and opened new avenues for creativity. As we delve deeper into the following sections, we will explore how these advancements have reshaped product design methodologies and examine their applications in diverse industries.
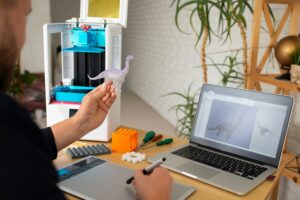
Historical Background
Early Origins of 3D Printing in the 1980s
In the realm of technological innovation, the roots of 3D printing can be traced back to the early 1980s. It was during this time that engineers and researchers began to explore the possibilities of creating three-dimensional objects from digital designs.
The concept emerged as a revolutionary approach, challenging traditional manufacturing methods that relied heavily on subtractive techniques. While these early endeavors were relatively primitive compared to modern standards, they paved the way for what would become one of the most transformative technologies in recent history.
The Development of Stereolithography (SLA) and Selective Laser Sintering (SLS)
Among the key milestones in the evolution of 3D printing technology were two groundbreaking processes: Stereolithography (SLA) and Selective Laser Sintering (SLS). SLA, developed by Chuck Hull in the mid-1980s, introduced a method where a liquid photopolymer resin is selectively cured using an ultraviolet laser to build layer upon layer until a solid object is formed.
This technique offered new possibilities for rapid prototyping and led to significant advancements in additive manufacturing capabilities. Around the same time, SLS emerged as an alternative approach pioneered by Carl Deckard.
This method involved selectively fusing powdered materials together using a high-powered laser. The ability to work with various materials such as plastics, metals, and ceramics opened up even more avenues for innovation in product design.
Adoption of 3D Printing in Rapid Prototyping
The adoption of 3D printing technology gained momentum primarily due to its impact on rapid prototyping processes. Traditional prototyping methods involved lengthy lead times and costly tooling expenses that often hindered iterative design iterations. With the advent of additive manufacturing techniques like SLA and SLS, designers and engineers were able to create physical prototypes directly from digital models in a fraction of the time.
This accelerated product development cycles, enabling more iterations to fine-tune designs while significantly reducing costs. Rapid prototyping became a game-changer for industries ranging from automotive to consumer electronics, where the ability to quickly validate designs and identify potential issues before mass production proved invaluable.
Furthermore, the flexibility afforded by 3D printing allowed for complex geometries that were previously unattainable using traditional manufacturing methods. As a result, product design evolved into a more iterative and efficient process that embraced the principles of accuracy, speed, and cost-effectiveness.
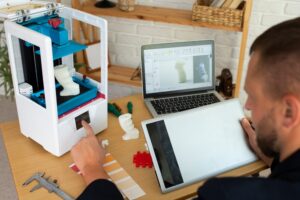
Advancements in Material Science for 3D Printing
Introduction to different types of materials used in 3D printing
When it comes to 3D printing, a myriad of materials has emerged, each with its unique properties and applications. Thermoplastics, such as ABS (Acrylonitrile Butadiene Styrene) and PLA (Polylactic Acid), are commonly used due to their low cost, ease of printing, and versatility.
These materials are ideal for prototyping and producing consumer goods. Photopolymers, on the other hand, exhibit excellent detail resolution and are often employed in stereolithography (SLA) printers.
Metals like titanium, aluminum alloys, and stainless steel have revolutionized industries such as aerospace and healthcare by allowing the production of lightweight yet strong components. Ceramics offer high-temperature stability and electrical insulation properties that prove valuable in electronics manufacturing.
Innovations in material properties for enhanced functionality and durability
As 3D printing technology has advanced, so too have material properties to meet the ever-growing demands of various applications. High-strength materials specifically designed for load-bearing applications have been developed to withstand immense pressure or stress without compromising structural integrity. These advanced materials include carbon fiber-reinforced composites that offer exceptional strength-to-weight ratios or glass-filled nylon polymers renowned for their toughness.
Such innovations enable engineers to fabricate functional end-use parts with remarkable durability. Another area of innovation lies in flexible materials tailored for intricate designs and complex geometries.
These elastomers possess remarkable elasticity while preserving dimensional accuracy during the printing process. They find extensive use in industries like fashion design where flexibility is crucial for wearable items such as shoes or garments that require both comfort and aesthetics.
The ability to print objects using a diverse range of materials not only expands the possibilities but also demonstrates how 3D printing has progressed beyond prototyping towards large-scale production. With ongoing research and development, we can expect even more groundbreaking materials to emerge, further broadening the horizons of additive manufacturing.
Integration with Computer-Aided Design (CAD)
The Powerful Nexus between CAD and 3D Printing
The seamless integration of Computer-Aided Design (CAD) and 3D printing has revolutionized the product design landscape, enabling designers to bring their wildest imaginations to life with astonishing precision. CAD software serves as the visionary’s virtual canvas—a digital platform where ideas take shape, dimensions are meticulously defined, and form meets function.
With CAD, designers can create intricate digital models that serve as blueprints for 3D printers to materialize into tangible objects. This transformative synergy between CAD and 3D printing empowers designers to transcend traditional design constraints and unlock an unprecedented realm of possibilities.
Precision in Digital Modeling: Measurements and Specifications
One of the key strengths of CAD software lies in its ability to create digital models with unparalleled accuracy in measurements and specifications. Designers can input precise dimensions, angles, curves, tolerances, and other intricacies necessary for the intended product’s functionality or aesthetic appeal.
Through meticulous attention to detail within the virtual environment, every aspect of the design is captured flawlessly before it enters the physical realm through additive manufacturing processes. This level of precision ensures that each printed iteration maintains fidelity to its original digital counterpart.
Optimizing Designs for Additive Manufacturing Processes
CAD software also plays a vital role in optimizing designs specifically for additive manufacturing processes. Unlike traditional manufacturing methods that often involve subtractive techniques like cutting or drilling from solid materials, 3D printing relies on building layer upon layer of material until the entire object is formed. This demands a unique approach in design optimization.
CAD software provides tools and capabilities for hollowing out structures by creating intricate internal geometries that maintain structural integrity while reducing weight and material usage. Furthermore, designers can generate support structures that provide stability during printing but are easily removable once the object is complete.
These optimizations allow for efficient use of materials, minimize post-processing efforts, and enhance the overall performance of the printed products. In essence, CAD software acts as a bridge between imagination and reality in the realm of 3D printing.
It empowers designers to translate their concepts into precision-engineered digital models, optimizing them for additive manufacturing processes to achieve remarkable results. This integration has not only expedited product development cycles but has also expanded the boundaries of what can be achieved through innovative design thinking and advanced manufacturing technologies.
Iterative Design Process Enabled by Rapid Prototyping
Unleashing Creativity and Enhancing Product Development
Rapid prototyping, facilitated by 3D printing technology, has revolutionized the traditional product design process, introducing a dynamic and iterative approach. This methodology allows designers to quickly create physical prototypes in a matter of hours or days, as opposed to weeks or months with conventional manufacturing techniques. By leveraging the power of additive manufacturing, product designers can bring their ideas to life more rapidly than ever before.
Benefits of using rapid prototyping through iterative design cycles
The utilization of rapid prototyping through iterative design cycles offers numerous advantages that significantly impact the product development landscape. Firstly, it enables designers to test multiple design iterations swiftly and efficiently. This ability to explore various concepts without lengthy delays empowers them to refine their designs in real-time, leading to enhanced functionality and aesthetics.
Furthermore, rapid prototyping substantially reduces costs when compared to traditional manufacturing methods. In the past, creating multiple prototypes involved substantial expenses due to tooling fabrication and setup costs for each iteration.
However, with 3D printing technology at hand, designers can produce prototypes directly from digital models without requiring expensive tooling or molds. This cost-effective approach not only benefits small businesses but also large-scale manufacturers seeking to streamline their development processes.
Overall, the iterative design process enabled by rapid prototyping allows for increased flexibility and efficiency in product development. Designers can experiment with different concepts swiftly while minimizing costs associated with multiple physical prototypes – an invaluable capability that propels innovation forward in countless industries.
Customization and Personalization Opportunities
Exploring the potential for mass customization using additive manufacturing technologies
In the realm of product design, customization and personalization have become increasingly important factors in consumer preferences. Additive manufacturing, with its ability to create intricate designs and complex geometries, offers a revolutionary solution for mass customization. By leveraging the power of 3D printing, companies can now tailor their products to individual customers’ preferences while still maintaining cost-effective production processes.
The flexibility provided by additive manufacturing allows for the creation of unique variations of a product without incurring excessive setup costs associated with traditional manufacturing methods. This opens up new avenues for businesses to reach niche markets or accommodate specific customer needs.
Case studies on personalized consumer products created through customization
The implementation of customization in consumer products has already yielded remarkable success stories. One such example is the footwear industry, where companies like Nike have embraced 3D printing technology to offer personalized sneakers tailored to each customer’s unique foot shape and size. By utilizing additive manufacturing processes, Nike has been able to provide an unparalleled level of comfort and fit for their customers, leading to increased brand loyalty and customer satisfaction.
Another noteworthy case study comes from the jewelry sector, where companies like Shapeways allow consumers to design their custom jewelry pieces using intuitive online platforms. Customers can select from a range of materials and customize every aspect of their jewelry’s design, resulting in truly one-of-a-kind pieces that reflect their style and taste.
These examples demonstrate how 3D printing enables businesses to tap into the growing demand for customized products across various industries. The ability to offer individualized experiences not only adds value but also fosters stronger connections between brands and consumers.
By harnessing the potential of additive manufacturing technologies, companies can redefine traditional notions of mass production by shifting towards mass customization models that cater to each customer’s unique preferences. This paradigm shift in product design and manufacturing opens up a world of possibilities for businesses, ultimately enhancing customer satisfaction and driving innovation in the market.
Conclusion
The evolving role of 3D printing in product design has revolutionized various industries by offering unprecedented opportunities for innovation and efficiency. From its origins as a rapid prototyping tool to now being an integral part of industrial production processes, 3D printing has demonstrated remarkable potential in transforming how products are designed and manufactured. As material science continues to advance and collaboration between software developers and manufacturers strengthens, we can anticipate even greater breakthroughs in additive manufacturing technology.
With each passing year, we move closer to a future where customization is commonplace, mass production is more agile than ever before, and creative boundaries are continually pushed. The possibilities offered by 3D printing are boundless and inspire optimism for a future where imagination knows no limits.