3D printing has opened up new possibilities for custom instrument design in the world of music. From unique guitar bodies to custom drum shells, 3D printing is transforming the way instruments are designed and produced. In this article, we will explore the use of 3D printing in music, including its advantages, challenges, and future trends.
Advantages of 3D Printing in Instrument Design
Customization
One of the key benefits of 3D printing in instrument design is its ability to provide greater customization. Using 3D printing, musicians can create unique and personalized instrument designs that are tailored to their specific needs and preferences. This can help to improve playability, sound quality, and overall performance.
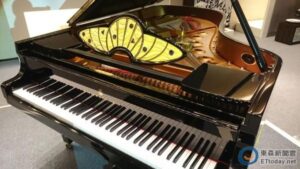
Design Flexibility
3D printing also allows for greater design flexibility in instrument design. With traditional manufacturing methods, certain design elements may be difficult or impossible to produce. However, with 3D printing, designers can create intricate and complex shapes and structures that would be difficult to achieve using traditional methods.
Improved Quality Control
3D printing allows for greater quality control in instrument design. With traditional manufacturing methods, there may be variations in the quality of individual components or instruments. However, with 3D printing, each component or instrument can be produced to precise specifications, leading to greater consistency and quality.
Reduced Waste
Finally, 3D printing can help to reduce waste in instrument design. With traditional manufacturing methods, a significant amount of material may be wasted during the production process. However, with 3D printing, materials can be used more efficiently, resulting in less waste.
Challenges and Considerations
While 3D printing offers many benefits in instrument design, there are also challenges and considerations to keep in mind. Here are some of the key challenges:
Cost: The cost of 3D printing technology can be high, particularly for large-scale instrument production. This can make it difficult for some musicians and manufacturers to adopt 3D printing as a key technology in their instrument design needs.
Limited Materials: The materials that can be used in 3D printing are currently limited compared to traditional manufacturing methods. This can make it difficult to achieve certain design elements or to produce instruments with certain sound qualities.
Regulations: There may be regulations in place in some jurisdictions that require musical instruments to meet certain safety or environmental standards. This can make it difficult to adopt 3D printing in instrument design, particularly for larger-scale production.
Future Trends in 3D Printing and Music
As 3D printing and music continue to evolve, there are several future trends that are emerging in the industry. Here are some of the key trends:
Customization
As mentioned earlier, customization is a key benefit of 3D printing in instrument design. This trend is likely to continue, with musicians and manufacturers increasingly using 3D printing to create unique and personalized instrument designs.
Sustainable Materials
The use of sustainable materials in 3D printing is also an emerging trend in instrument design. With musicians and manufacturers becoming more environmentally conscious, there is growing interest in using sustainable materials in instrument production.
Integration with Smart Technology
The integration of 3D printing with smart technology is also a growing trend in instrument design. By incorporating sensors and other technology into 3D printed instruments, musicians can create instruments that are more responsive and adaptable to different playing styles and environments.
Exploring the Possibilities of Custom Instrument Design
3D printing is already being used to create a wide range of custom instruments, from unique guitar bodies to custom drum shells. Here are some examples of how 3D printing is being used in instrument design:
Custom Guitar Bodies
3D printing is being used to create custom guitar bodies with unique shapes and designs. This can help to improve playability and sound quality, as well as create visually striking instruments.
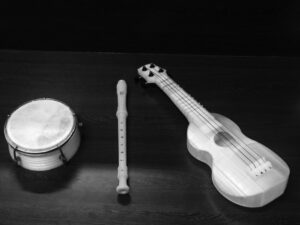
Custom Drum Shells
3D printing is also being used to create custom drum shells with intricate designs and patterns. This can help to create unique and personalized sounds, as well as visually striking instruments.
Custom Wind Instrument Mouthpieces
3D printing is being used to create custom wind instrument mouthpieces with unique shapes and designs. This can help to improve performance and sound quality, as well as create personalized instruments that are tailored to the specific needs of the musician.
Another possibility is in the creation of 3D printed musical instruments themselves. While there are already a few examples of 3D printed musical instruments, such as 3D printed violins and flutes, there is still significant potential for innovation in this area. 3D printing could be used to create entirely new types of instruments with unique shapes and designs, or to create instruments that are more ergonomic and comfortable to play.
There is also potential for 3D printing to be used in the repair and restoration of musical instruments. For example, 3D printing could be used to create custom replacement parts for vintage or rare instruments, which can be difficult or impossible to find using traditional methods.
While there are many possibilities for 3D printing in music, there are also several challenges that must be addressed. One major challenge is the cost of 3D printing technology, which can be prohibitively expensive for many musicians and manufacturers. In addition, there are limitations to the materials that can be used in 3D printing, which can make it difficult to achieve certain design elements or sound qualities.
Another challenge is the need for expertise in 3D design and printing. While the technology has become more accessible in recent years, there is still a learning curve for musicians and manufacturers who are new to 3D printing. Additionally, there may be regulations in place in some jurisdictions that require musical instruments to meet certain safety or environmental standards, which can make it difficult to adopt 3D printing in instrument design and production.
Conclusion
The use of 3D printing in instrument design is transforming the way musicians and manufacturers create and produce instruments. With greater customization, design flexibility, quality control, and reduced waste, 3D printing offers many advantages over traditional manufacturing methods. While there are challenges and considerations to keep in mind, the future possibilities are endless. With the integration of smart technology and sustainable materials, 3D printing has the potential to help musicians create instruments that are more responsive, adaptable, and environmentally friendly. As technology continues to evolve, we can expect to see even more innovation and growth in the use of 3D printing in instrument design.